- Home
- Services
- Machining
On Demand CNC Machining Services
Looking for a competitive advantage, rapid turnaround supplier for your CNC machining project? Innovacasts is an expert in CNC machining service in China for both prototypes and machined parts of end-use.
We offer a wide range of CNC machining services including milling and turning of various materials, as well as drilling, tapping, EDM (Electrical Discharge Machining), and wire EDM. Our ISO 9001 certified production process, combined with professional experiences and advanced CNC machines ensures your parts are made right the first time, every time.
We Offer A Differentiated Custom Machining Service
Prototype Machining for Design Verification and Engineering Testing
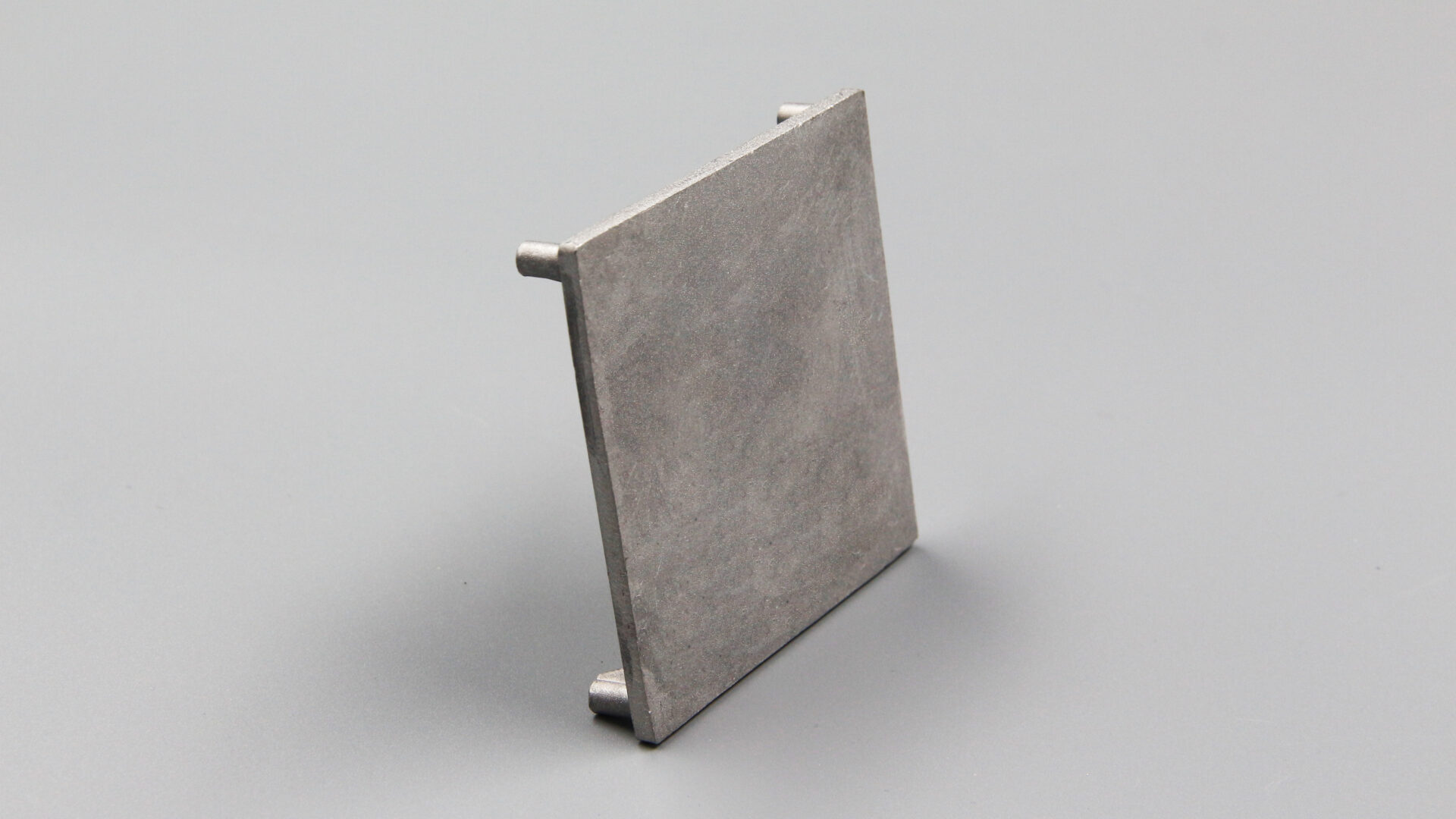
Custom Machining for Low-volume Production of End-use Parts
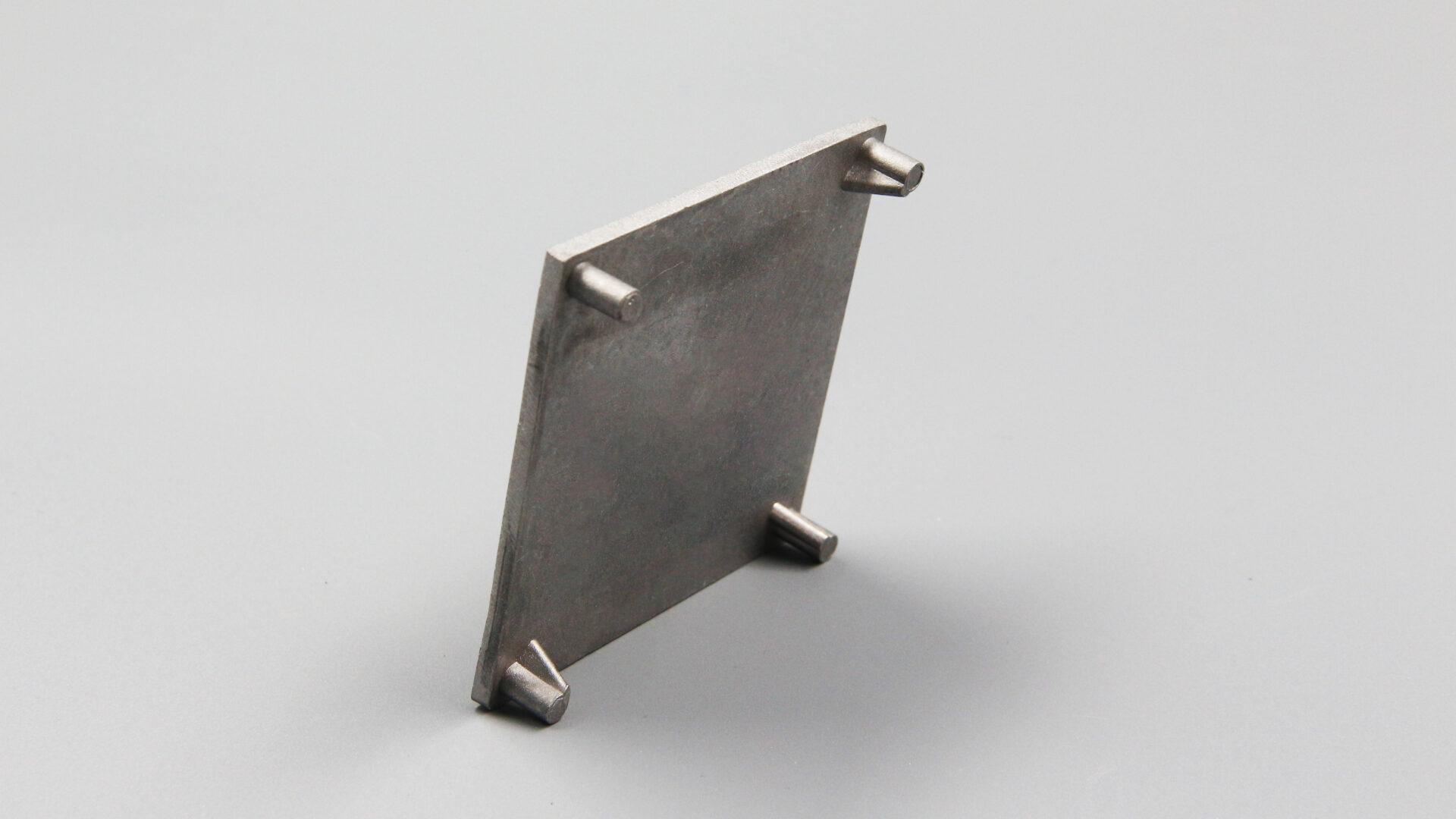
Put Your CNC Parts Into Production Today.
CNC Machining Tolerances
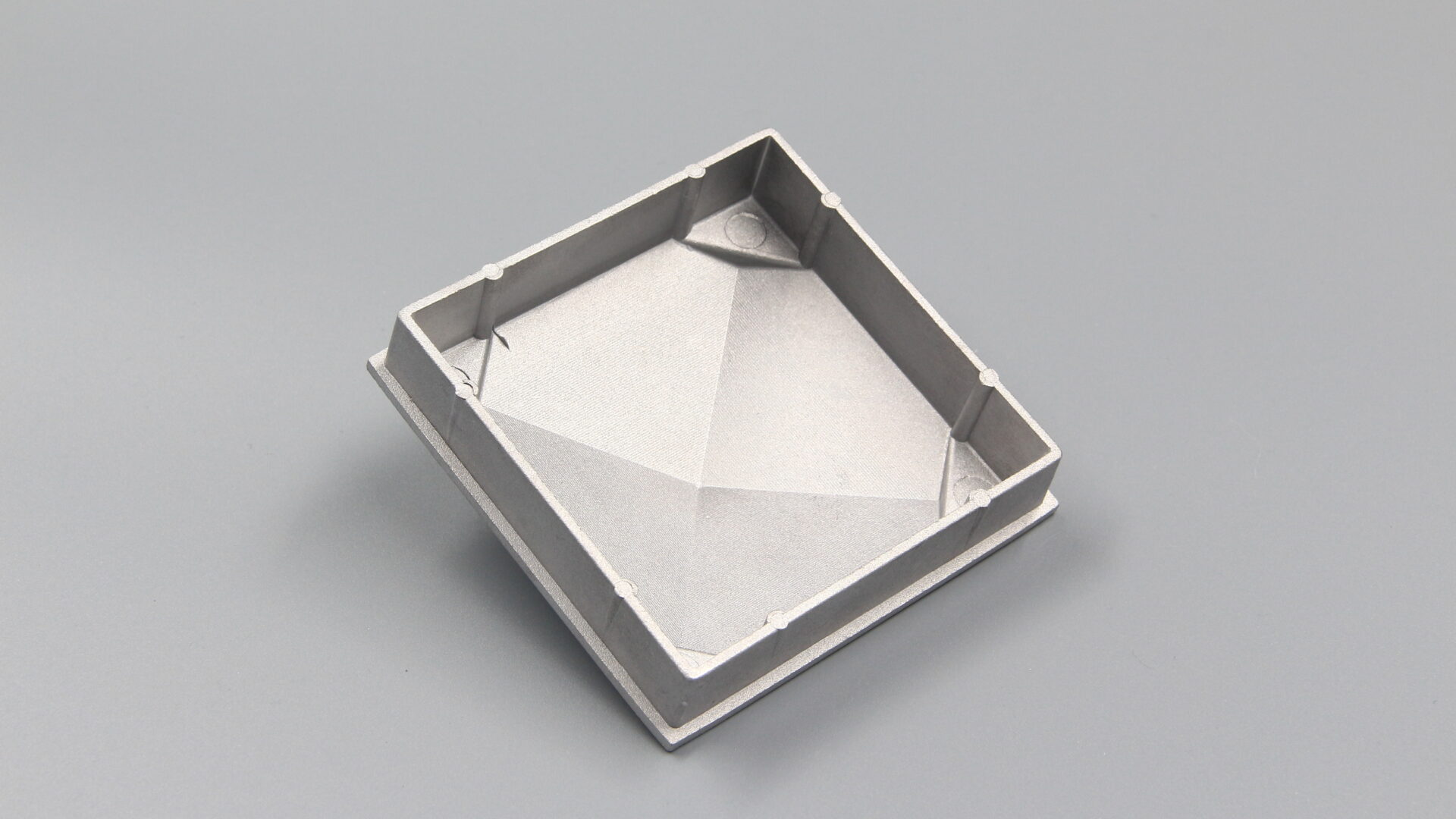
We will custom-manufacture products to suit your needs
-
01.
Inquiry
Please provide as much information as possible about the parts and your requirements.
-
02.
Proposal
We will provide you with our proposal for a product that meets your requirements.
-
03.
Order
Production will begin according to the agreed-upon specifications and terms.
-
04.
Production & Delivery
Your product will be manufactured under our strict quality control system.
A Quick Guide To Designing CNC Machined Parts
Optimize your designs to avoid unnecessary machining features, limit part complexity, help reduce CNC machining costs and time, and create machined parts faster and more efficiently.
As large an internal radius as possible
Any internal cut will generate a fillet that is half the diameter of the tool used. Milling with smaller tools takes a long time and we recommend that the radius should be greater than 1/3 of the depth of machining. The best bet is to relieve internal corners or allow for as large an internal radius as possible on mating part designs and use the same radius on all inside edges so that the same tool can be used throughout the CNC machining processes.
Avoid overly deep cavities, grooves and holes
The depth of the cavity and groove is usually related to the diameter of the tool used to make the internal fillets, and a good rule of thumb is to keep the cavity depth 3 – 4 times the tool diameter or the groove depth less than 4 times the feature width. Whether blind holes or through holes, the recommended maximum depth is 4 times the diameter and the minimum hole diameter is 1 mm, and it is recommended to design standard size holes. With a standard drill, holes can be machined quickly and with high precision; for non-standard holes, using an end mill will increase costs.
Avoid thin walls
As with tall walls, vibration increases when machining thin features. As a guide, the minimum thickness of thin-walled metal parts should be 0.5-0.8 mm, and the minimum thickness of plastic parts should be 1.0- 1.5 mm. If the walls are for supporting action or taller features, the wall thickness should be increased to avoid vibrations during CNC machining processes.
Avoid small or raised text
You may need to mark parts with part numbers or company names. Adding text looks really cool in the custom CNC machining, but is time-consuming to process; electrochemical etching or laser marking is usually better. If you must cut text, choose recessed rather than raised text whenever possible, keep it simple and large, with a font depth of no more than 0.3mm.
Stick to the standards for threads
Sticking to standard sizes is also important when creating threads. Length should be kept to a maximum of 3 times the nominal diameter of a hole. For blind hole tapping, it is preferable to add an additional length of at least 1/2 hole diameter at the root of the hole. You might also think about using inserts. threaded coils and brass nuts provide longer service life than bare threads, especially in soft materials such as aluminum or plastic, and are easy to install.