- Home
- Company
- Gravity Casting
What Is Gravity casting?
Gravity casting is among the oldest known processes for fabricating metals and metal alloys. It involves the pouring of molten metal from a crucible into a mold under only the force of gravity, without the use of pressurized gases, vacuums, or centrifugal force.
Small-scale molds used for this form of casting have most commonly been made of sand, tufa stone, and cuttlebone as well as charcoal and plaster as these materials are generally easy to shape (unlike iron or steel), do not break down when suddenly exposed to high temperatures (unlike glass, wood, or plastic), do not deform easily (unlike silicone) and are widely available.
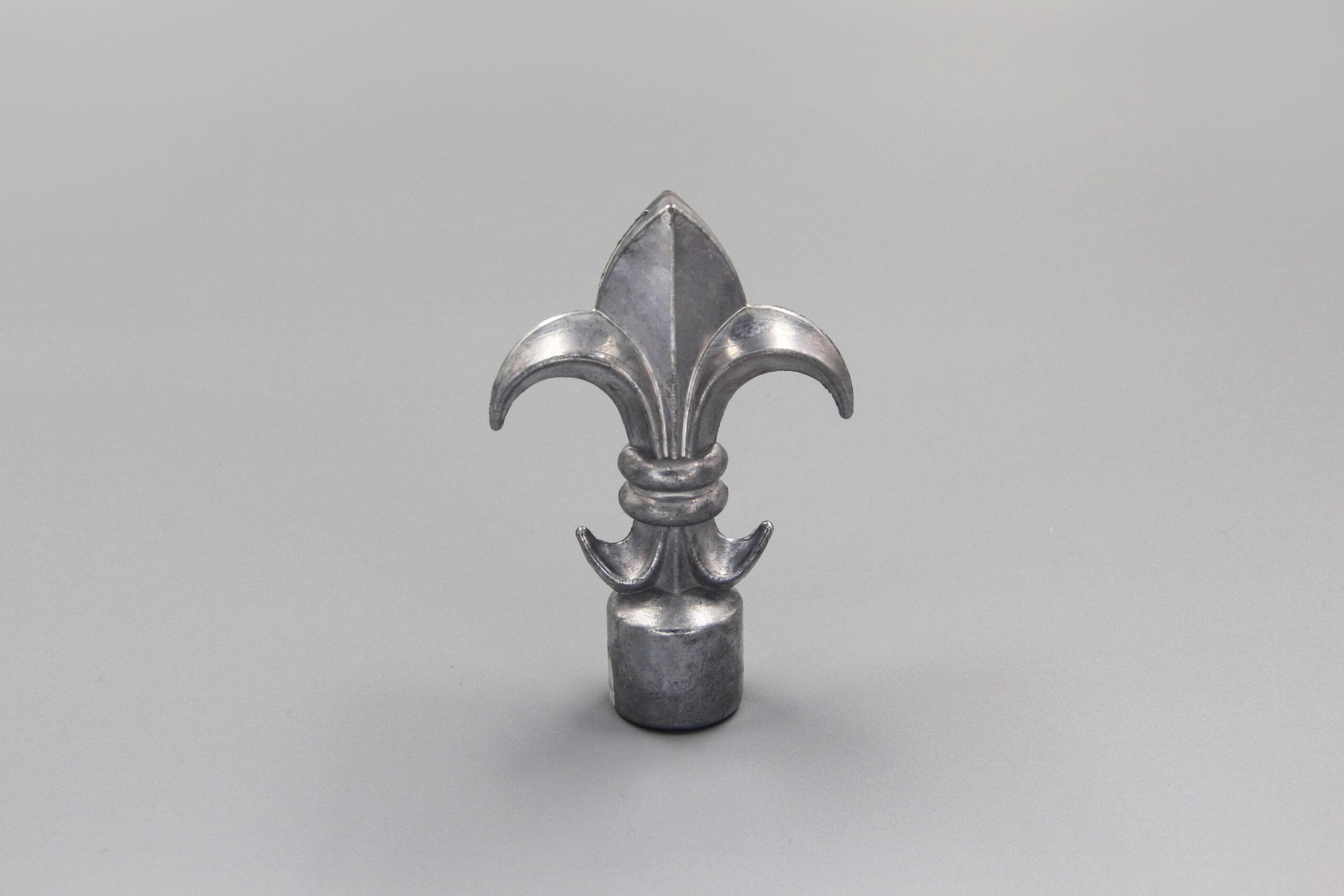
How Does Gravity Die Casting Differ From Other Types of Casting?
• In sand casting, compacted sand is placed around a wooden or metal pattern, and additional cores are inserted to create internal features. Molten metal is then introduced into the sand molds. The molds are subsequently fractured to extract the castings.
• In low-pressure die casting, molten metal is introduced into the mold under relatively low pressure, which helps reduce turbulence and air entrapment, resulting in higher-quality castings.
• In high-pressure die casting, die casting is a high-pressure casting method where molten metal is forced into a mold cavity under high pressure.
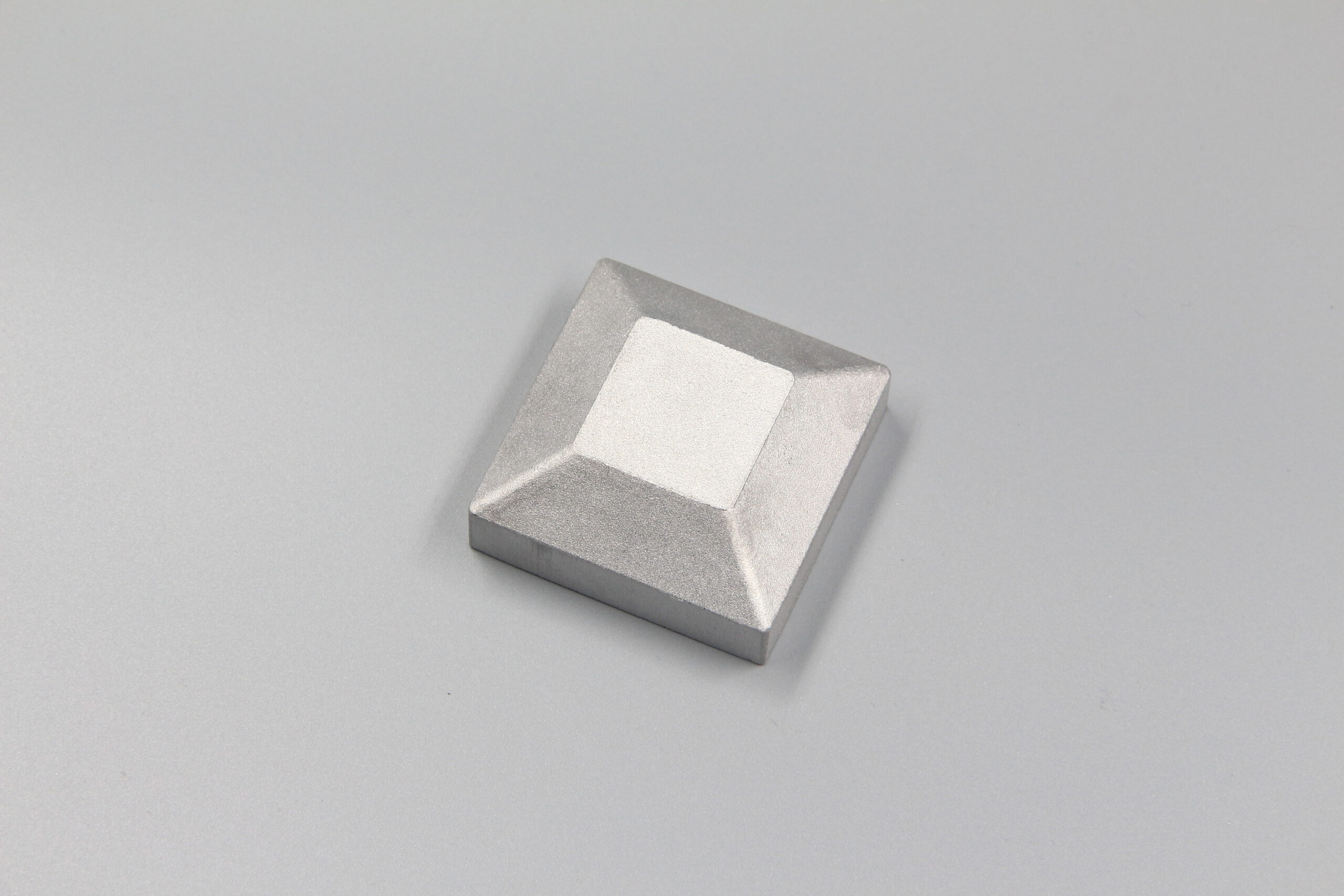
Gravity Die Casting Also Called the Lost Wax Process
What Is the Importance of Gravity Die Casting in Manufacturing?
The importance of gravity die casting in manufacturing lies in its capacity to deliver moderate dimensional accuracy and consistency. This technique enables the creation of complex parts with less energy consumption than high-pressure casting due to gravity being the source of pressure.
Gravity die casting offers several advantages over other casting methods, such as sand casting, low-pressure casting, high-pressure casting, and investment casting. Unlike sand casting, which is suitable for prototypes and small-volume production, gravity die casting strikes a balance between moderate dimensional accuracy and production volume. It is well-suited for demands ranging from 250 to 50,000 units per annum. Its cast iron or steel molds provide greater accuracy and cost-effectiveness compared to sand casting’s wooden or resin patterns.
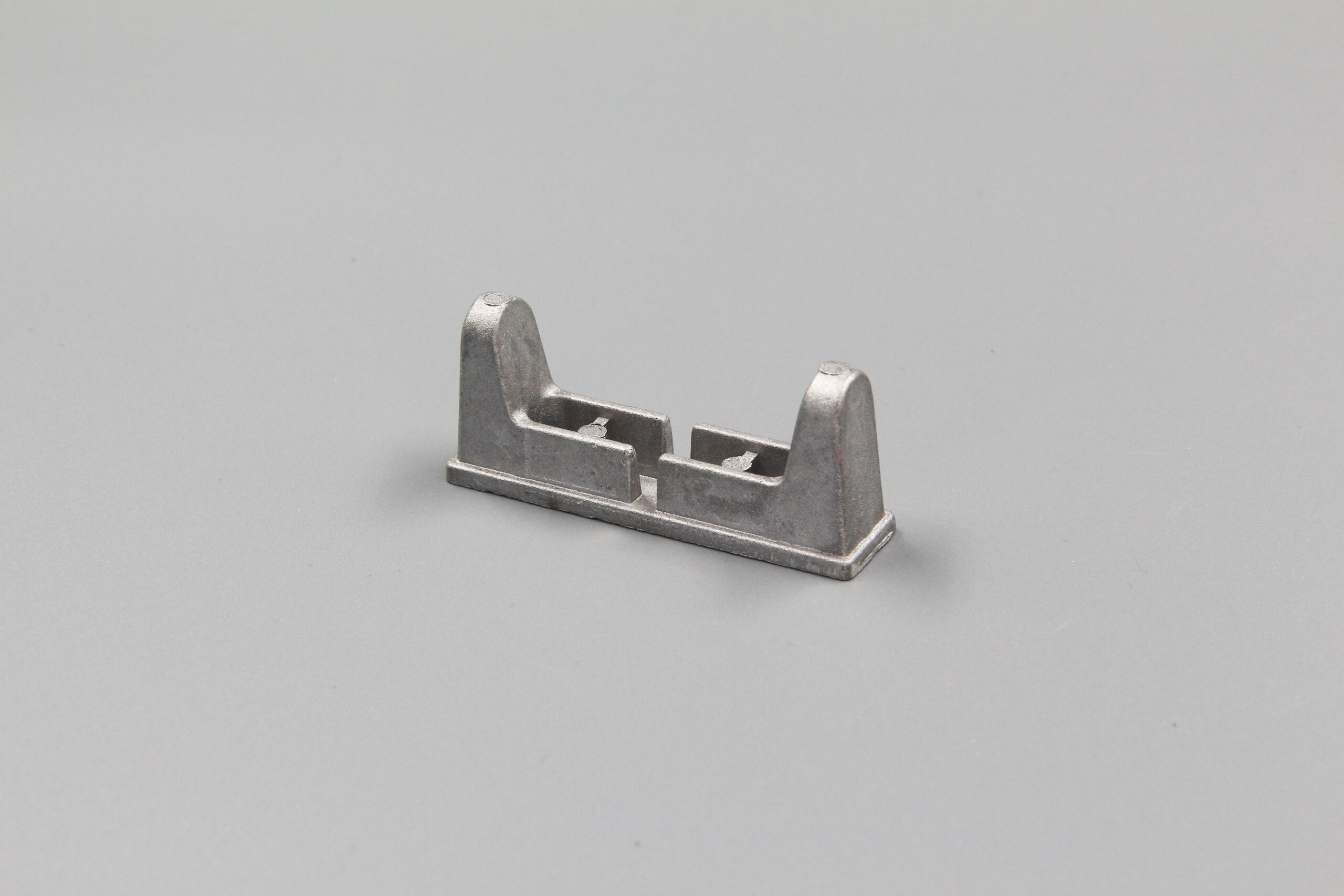
Which Industries Use the Gravity Die Casting Process?
Gravity die-cast components are used in every industrial domain, including: automotive, marine, defense, architectural and construction applications, electronics, complex machinery, and consumer appliances.
How Does Gravity Die Casting Work?
Gravity casting works by allowing molten metal to flow gently into a permanent mold under the influence of gravity alone. Vents and risers on the mold allow the escape of gasses and the complete filling of the mold with minimal porosity due to trapped gasses. The liquid metal solidifies quickly because the mold is also made of metal, which rapidly conducts heat away from the just-poured casting.
Every day we work collaboratively to find new opportunities and discover unique, high-value solutions for your product manufacturing.